Automated Reactor Rethreading System
Developed an innovative semi-automated system for rethreading tungsten filaments in chemical vapor deposition reactors, significantly reducing downtime and improving operator safety.
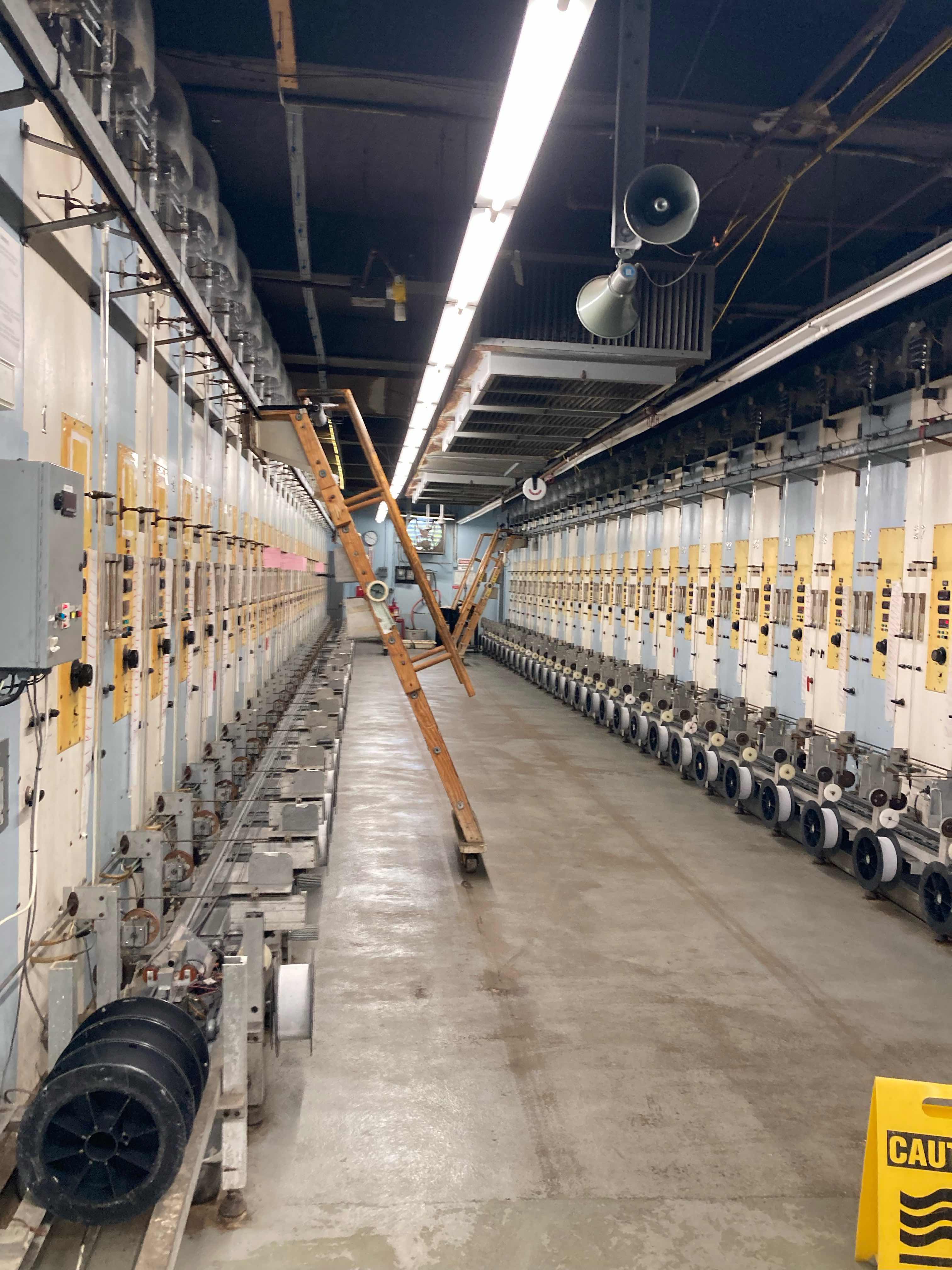
The Challenge
Specialty Materials, a leading manufacturer of boron fiber, faced significant operational challenges with their chemical vapor deposition (CVD) reactors. The existing manual process of rethreading tungsten filaments when reactors went offline was time-consuming, ergonomically challenging, dangerously hot, and potentially hazardous due to the use of liquid mercury. This process required operators to climb a ladder 12 feet into the air and work near 1,300°C reactor tubes, leading to extended reactor downtime and safety concerns. The challenge was to design a system that could automate this process while ensuring operator safety and maintaining production quality.
Solution
Led a cross-functional team to develop a semi-automated rethreading system incorporating several innovative features: • Designed a track-and-trolley mechanism allowing filament handling at operator hand-height • Implemented an Arduino-based control system with custom C++ programming • Created a precision drive system using stepper motors and custom 3D-printed components • Developed an integrated alarm system to detect reactor failures • Engineered a modular design compatible with existing reactor infrastructure • Incorporated safety features including emergency stops and visual/audio alerts The system was designed to operate in challenging conditions including high temperatures (200°C) and corrosive environments, while maintaining precise control over the delicate tungsten filament.
Outcome
The project delivered significant improvements to the manufacturing process: • Reduced reactor downtime by 71.9% (from 50.4 to 14.1 minutes) • Improved operator safety by eliminating the need for ladder climbing • Decreased ergonomic risk (REBA score improvement from 10 to 4) • Projected annual savings of $196,756 per facility • Created comprehensive documentation including CAD drawings, electrical schematics, and standard operating procedures • Developed a proof-of-concept prototype demonstrating system viability The project successfully balanced automation with practical operational requirements, creating a system that could be implemented across multiple reactor units while maintaining reliability and safety standards.
Technologies Used
- Arduino Uno microcontroller with C++ programming
- SolidWorks for mechanical design and 3D modeling
- Custom-designed control systems for precision motor control
- Advanced sensor integration for process monitoring
- Industrial-grade stepper motors and actuators
- Custom 3D-printed components for specialized applications
- Integrated safety systems and alarm protocols
Project Gallery
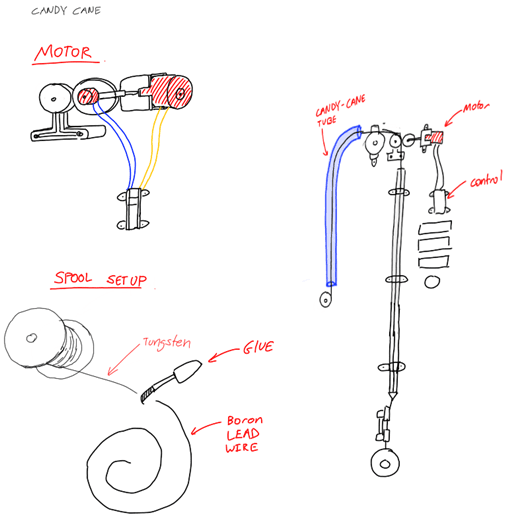
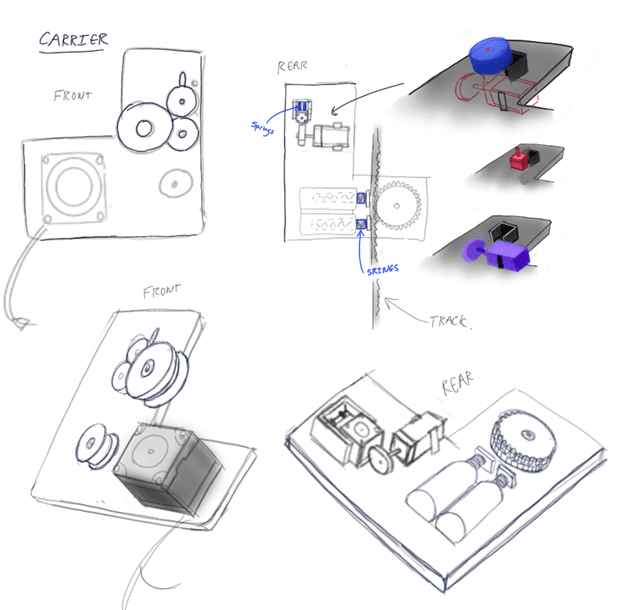

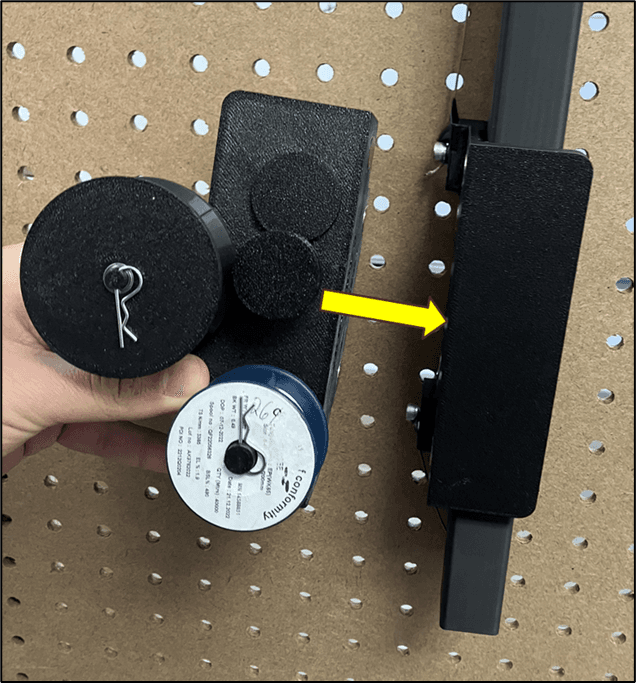
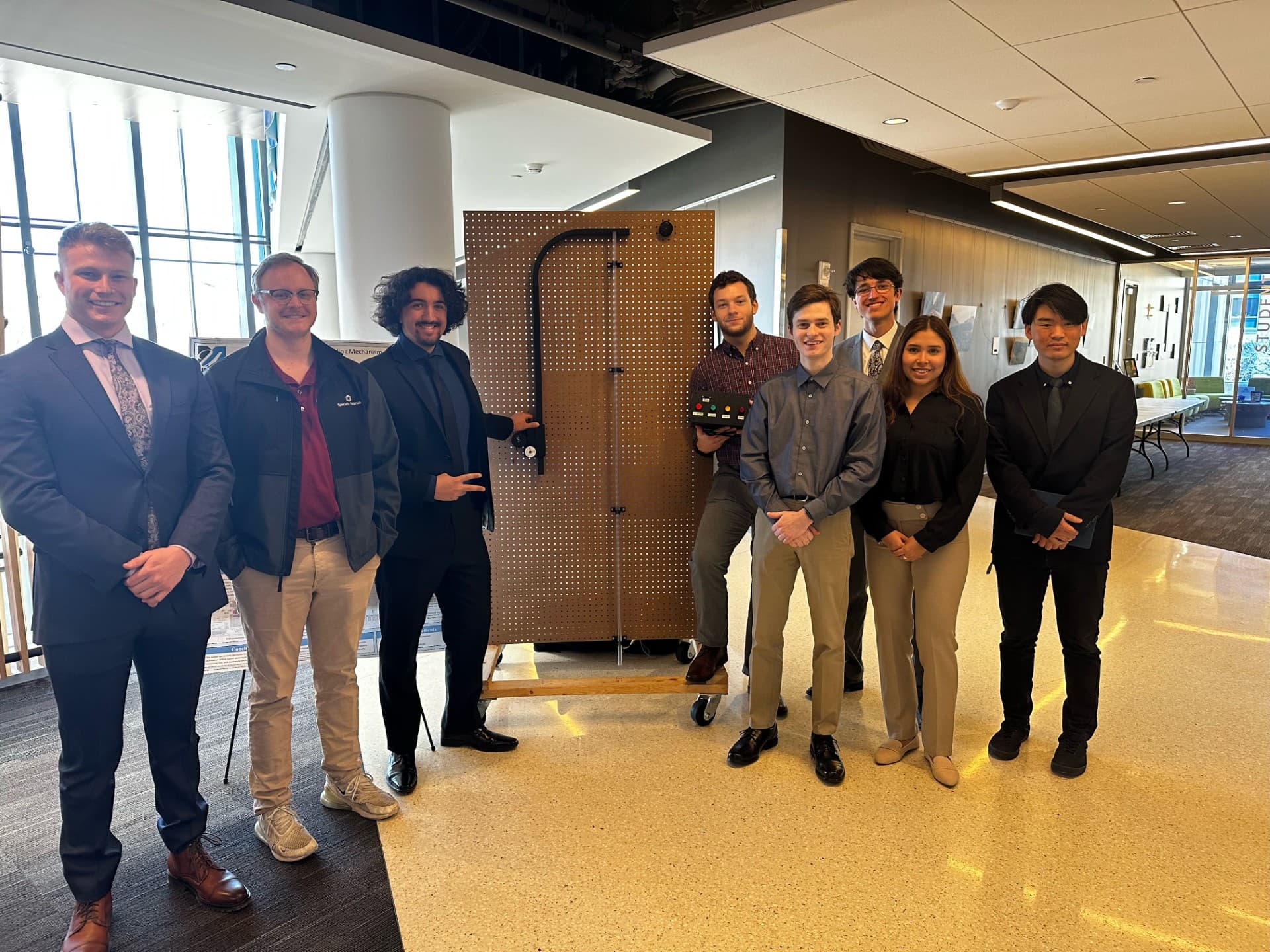